$100k averted with condition monitoring of critical assets
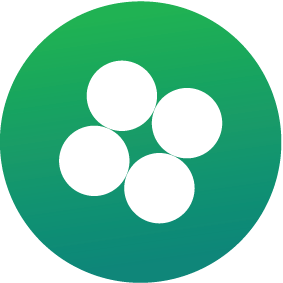
Summary
EfficientSee designed and implemented a Condition Monitoring system allowing the customer for the first time to analyse the vibration performance of their key assets in real time, over a sustained period.
In large organisations energy management often comes second to asset management (which is completely OK by the way) but this should not mean that energy is ‘forgotten’ or that it’s not important. Many assets connect with energy at some level, whether it’s a simple as illuminating the structure or as integral as power the motor for the machine. So, it’s not a case of either or, but both need to be managed well and, in many cases, there is a symbiotic and inseparable relationship between assets and energy.
At the end of the day it’s the assets the enable the delivery of their service or product and therefore must always come first in the order of priority. Nevertheless, the goal is to have assets functioning optimally, reliably and cost-effectively and energy performance can be a good indicator of that.
This case study is a great example of how energy and asset management are (or need to be) intertwined. Condition monitoring can include data capture and analysis of variables such as vibration, temperature, speed as well as current and power. All give clues to asset performance and condition.
A poor performing electrical asset tends to be less reliable as well as being less efficient, which one way or another leads to higher costs to run the asset. These costs accumulate through increased running and maintenance expenses or worst still through increased failures and downtime.
Asset management is all about reducing risks and the condition monitoring solution allows customers to be on the front-foot and proactive rather than reactive.
If we think about a clean, reliable and affordable energy future, this solution ticks the ‘reliability box’.
Challenge
Large 200 to 315 kW motors driving cooling or combustion fans, 24 hrs per day, critical to production. The failure of any one motor resulting in lost production time, the discarding of product, and significant repair/replacement costs.
Every motor and fan generates vibrations during operation. These vibrations can quickly exceed a permissible level due to unbalance, misalignment or resonances. An increase in the oscillation amplitude has a negative effect on the motor / fan condition and reduces the lifetime and increases the risk of failure.
The result if not monitored: unexpected failures, unplanned outages and shorter lifetime.
Specifics
- Large 200 to 315 kW motors driving cooling fans, 24 hrs per day, critical to production
- Four channel Vibration Diagnostic System for the capture, analyse, reporting and alarming of the vibration data
- Temperature Sensor able to be located on a Fan bearing or Motor bearing
- Speed reference directly from the Variable Speed Drive or from an inductive speed sensor
- Enclosed within an environmental cabinet alongside the motor.
Solution
EfficientSee designed and implemented a system utilising a four channel Vibration Diagnostic System and Vibration Sensors, allowing the customer for the first time to analyse the vibration performance of their key assets in real time, over a sustained period.
Facilitated collaboration between internal and external stakeholders to bring the necessary elements together, to provide a fully installed, commissioned and integrated turn-key solution.
Key Services
- Articulated the customers need
- Aligned an appropriate third-party diagnostic system
- Designed a system tailored to the customers environment
- Identified, sourced, managed and instructed the require technical trades
- Integrated the system into the existing site network
- Performed the Job Safety Analysis and detailed the impact to production
- Installed and commissioned the system
- Trained the maintenance personnel on the system
- All as a turn-key risk-free project for the customer.
Outcomes
People
Maintenance decisions are able to be made with confidence, with the ability to analyse and compare the resultant vibration effect to the system in real-time and on demand.
Planet
Extended asset life.
Prosperity
Anecdotally we can point to $100k of costs related to failures that should now be avoided or averted with the condition monitoring system in place.